企鹅电竞企鹅
/ Products Classification 点击展开+- 【48812】vivo X Fold折叠屏零件修理价出炉 内屏更换费用5080元职业最高
- 液晶显示器出现水波纹怎么办
- 【48812】好“芯”才有好Mini LED!海信电视E8系列重磅上台
- 争抢 “新赛道”:5G定位加速商用
- 【48812】电子设备屏幕碎了莫慌先自己判别下不要急着换以防被忽悠
联系我们
上一期的内容是车载显示屏的液晶相关的原理,智能座舱显示屏相关原理---第一篇。本期讲讲背光相关的内容,很多人其实不知道,显示屏背光是干啥用的,以为液晶偏转过后就有对应的亮光显示,其实液晶偏转那里仅仅是色彩显示,并没有亮度。
我举一个最简单的栗子,你在阳光下把手机或者电视亮度调到最低,是不是基本就看不清显示屏里面的内容了。
所以这里的背光就是跟整个液晶显示模组提供亮度的一个模组,里面涉及到的材料还不少,本期慢慢来说。
这样你就简单想象一下,你家里熄火了,你点了一根蜡烛在家里,此时发现一个什么问题,是不是靠近蜡烛的地方光亮最集中,最亮,其他空间的亮度是不均匀的,此时液晶显示屏的背光也会遇到此类的问题,如果是LED的光直接上来,就会发现个别地方特别亮,其他地方不亮,不均匀。
背光模组根据光源布置位置,可以分为侧光式和直下式两种,对于中小尺寸液晶显示面板基本都采用侧光式结构,以减少LCM 的整体厚度。侧光式背光模组根据胶铁结构形式,有全胶框背光、胶铁组装式背光和胶铁一体式背光三种形式。
根据背光模组自身是否带有LED 灯源,又可分为无光源和有光源两种形式,但是结构基本一致。如下图所示,即常用的胶铁组装式背光。无光源背光模组只是将LED 布置在主FPC 上,后期组装时再扣入背光模组的灯槽中。如此,可以减少节省一定的成本。
而无论是何种形式的背光,其原理都是一致的,即用胶框和铁框作为结构件,以贴覆各个膜材。各膜材的混合使用是为了形成均匀的、高亮度的面光源。各零件使用的材质及具体作用如表2-1 所示。
从成本角度考虑,背光模组三个重要组成部分是光源、导光板、光学膜,占整个背光模组成本的73%。
侧发光LED 发出所需亮度和颜色(一般白色)的光, 经过导光板的作用,把侧面光源转换成我们正视的面光源→ 大部分光线折射到正面, 小部分光线通过反射膜的作用,反射后被再次利用→光线经过下扩散膜的扩散作用被完全打散,使光线在整个平面相对平衡。
→经过下增光膜的棱镜聚集作用,使光线在横向或纵向得到增强→ 经过上增光膜的棱镜聚集作用,使光线在纵向或横向得到增强有时为了让画面的均一度更好,或遮盖轻微不良现象,也会使用到上扩散膜,光线被再次扩散打乱,画面显示的一致性更好。
LED:Light Emitting Diode.发光二极管,是一种固态的半导体器件,它可以直接把电能转化为光能。LED 的核心器件是一个半导体的发光二极管灯芯即晶片,晶片的一端附在支架上,一端是负极,另一端连接电源的正极,使整个晶片被环氧树脂封装起来。
半导体晶片由三部分组成,一部分是P 型半导体,在它里面空穴占主导地位,另一端是N 型半导体,在这边主要是电子,中间通常是1 至5 个周期的量子阱,在量子阱内电子跟空穴复合,然后就会以光子的形式发出能量,这就是LED 发光的原理。而光的波长也就是光的颜色,是有形成P-N 结的材料决定的。
通常液彩屏晶显示模组都使用侧发光(side view)白光LED。LED 由发蓝色光灯芯(LED Chip),塑胶框(Lead Frame),黄色填充物(Epoxy)和正负极封装组成。
背光模组的初始亮度和色坐标都取决于所使用的光源。在液晶显示的发展历程上,所采用的光源方式主要有LED、EL 与CCFL 三种。其性能对比如下:
体积小,质量轻;耗电量低,工作电压低,工作电流小;使用寿命长,一般可达10 万小时;亮度高,发热低;环保,符合RoHS 要求;可控性强,能实现各种颜色的变化。
液晶显示模组主要是以使用蓝光芯片加黄色填充物LED,即侧发光式白光LED。目前高端LED 主要以日本厂家为主,其次是韩国厂家和台湾厂家;大陆厂家也陆续有相关产品投入大批量使用。
导光板一般是由高透光性材质作为基板,背面印刷有规律性网点,能够将点或线光源转化做面光源的光学器件,它的结构和材料直接影响着背光源最终的亮度和均匀性。
导光板的原理:利用入光部的Serration 锯齿结构和底部网点把LED 发出的所有光线进行折射或反射,改变光线传播的方向,高效率地利用光线。
导光板的结构:如图2-12 所示。与扩散膜贴合一面,根据后处理不同,可以是光面、磨面、放电面或V-CUT 面。目前大多采用光面,无需后处理,成本低,但是表面较容易刮伤,不便于生产途中传送。磨面是在导光板注塑成型后用砂轮处理而成,放电面是放电后再抛光,效果像磨沙的玻璃。而V-CUT(精密机械刻画)是在导光板的光面上刻出V 型沟槽,可聚拢一定方向的光线,从而达到提高亮度的效果。
而与反射膜贴合一面为网点面,网点结构形式有半球形,圆锥形,棱锥形以及棱镜形。而使用较广的为半球形网点,一般面内有30~120 万个圆点,越远离光源的圆点越大,点与点之间的间距也越近。网点的尺寸和位置是利用光学仿真而设计的,其作用是破坏侧光在导光板内的全反射,使光线能从光面垂直射出。网点设计越好,能从导光板正面射出的光线越多,则背光亮度越高。
导光板基材一般选择:PC 或者PMMA ,聚甲基丙烯酸甲酯,其性能对比如下
目前中小尺寸导光板基本都是采用注塑成型生产的,随着导光板越做越薄,为了解决注塑成型的工艺困难,逐渐引入压缩成型工艺、Roll Stamping 工艺。而无论何种成型工艺,都需要基于一定的模具生产,整个工艺中最难的也正是模具的网点加工。
目前行业里,更多的厂商偏向于采用机械撞点来加工网点。但随着V-CUT技术不断地成熟,市场对高亮度液晶显示屏的需求也越发高涨,V-CUT 技术成为厂商争相追求的新技术,纷纷加入其技术的研发和设备的采购,相信不久V-CUT 导光板将会被广泛地应用。
PMMA:主要是日本三菱丽阳(Mitsubishi Rayon),住友(Sumitomo),库拉雷(Kuraray),台湾奇美化学,韩国世和等。
增光膜分正反两面,最小厚度为0.062mm。正面上形成间距为24~110μm,顶角90°~110°的长条状棱镜阵列,因而增光膜又被称为棱镜膜(Prism Film)。
经过光学仿真设计,合理设置增光膜表面的微结构的尺寸,使之如同全反射棱镜一般,能够把较大传播方向的光线集中到正面较小的角度内,提高正面辉度。现在所用的这种增光膜一般需要两张增光同时使用(沟槽方向互相垂直),才具备良好的增光作用。
增光膜主要以聚脂(PET)为原料,利用花纹模辊的制造。目前中国大陆还不能生产,做得最好的是美国的3M 公司,但是价格很高。此外,常用的供应商还有台湾的光耀和友辉。
研究表明、绝大多数消费者在多数时间观看电视角度的都在水平(x 轴)90 度垂直方向(z 轴)方向的范围内、超出该角度后°光线变暗。将光聚在消费者、在功耗不变的情况下提升了消费体验、同时还是液晶显示屏亮度大大提高。增光膜原理:在视角测试仪的视角图上,在观察者正面35 度左右光线被折射利用,其他光线被反射后再次被充分利用。
扩散膜是在PET 基材上,涂布光学粒子颗粒或玻璃微珠形成的(在结构上,不同厂家制作的扩散膜会有细微的区别,图例为惠合扩散膜结构)。这些颗粒的排列方式和密度决定扩散膜的雾化度和光学作用,使得扩散膜具备可修正从导光板射出光线的传播方向的作用,为液晶屏幕提供均匀的、柔和的光。而由于粒子的存在使扩散膜表面具有一定的雾度,还能遮蔽导光板上的微小缺陷或异物。
经过导光板转换的出光角度一般在55-60 度角方向,然后再经过扩散膜的光线、通过扩散膜内部的亚克力球、粗糙表面或扩散粒子其折射、散色,最终将光线均匀化。可以有效匀化光、遮盖不良。扩散膜一般选用PET,PC 等。
利用PMMA 扩散粒子,使光线产生无规律的折射,面光源产生有效的均一性。比如牛顿环现象经过扩散膜的处理,而得到减轻或完全消失。
在外观形态上,扩散膜一般一面为雾面,另一面为光面。组装时,贴附方式均为雾面向上,亮面向下(朝向导光板)。而扩散膜除了可以加在导光板的光面上,作为下扩散配合增光膜使用,也可以放置于增光膜上,作为上扩散使用。扩散膜放置的位置不同,对其性能要求的不尽相同,对于下扩散,要求具有高扩散率、高雾化度;对于上扩散,要求具有高光学透过率、低雾化度、防止Waving(眩影)、防止光学干涉等特性。
反射片原理:反射板的主要作用为将从导光板底部漏出的光反射回导光板再利用,以增加光的使用效率。
反射片类型:依照外观一般划分为白反与银反两种,反射片一般是白色镀银或涂布有CaCO3 、BaSO4、TiO2 的反射片,厚度通常65~230μm,反射率大于95%。有的公司也采用镀铝膜的塑胶片。
反射膜的主要作用就是尽可能高效地把光线反射到我们需要的面上。如果是黑白双屏显示模组,可以采用80%左右透过率的反射膜,如果是高亮彩屏显示模组就可取消反射膜。
此反射膜在单屏及彩屏显示模组上常用。光线的利用率越高越好,比如3M公司的ESR 双面镀银反射膜,反射率可达到98%以上。
此反射膜常用于黑白双屏显示模组,大约20%的光线透过反射膜,用在黑白屏显示所需亮度。比如SKC 公司的SW 系列。反射片类型说明
反射膜常用供应商,目前反射膜市场主要以3M,日本等供应商为主,韩国供应商为辅,大陆也陆续有相应供应商批量生产供货。
反射膜本身不含胶,组装方法有两种:一是直接放置于胶框上。由于导光板和胶框组装由卡扣固定,所形成的间隙用于放置反射膜。此种组装方式,反射膜具有一定的活动间隙,更能适应环境温冷变化。另一种组装方式是用双面胶将反射膜贴于胶框背面,此种组装方式,反射膜是固定的。
A. 常用双面粘性胶带,其作用是遮挡多余光线,形成设计需要的发光区域(lighting area);另外一个作用是利用其粘性把LCD 与BLU 背光源组装在一起,粘结液晶面板和背光模组,对于光线具有一定的反射作用,提高背光的利用率78%(黑白胶带);
B. 目前常用供应商包括美国3M,日本积水Seiksui,徳莎Tesa,Tapex 及国内力王、综研等。
C. 鉴于目前轻薄化设计,遮光胶带常用0.06,0.05,乃至研发阶段的0.03mm。
偏光板是使不具偏极性的自然光,产生偏极化,转变成偏极光,加上液晶分子扭转特性,达到控制光线的通过与否,从而提高透光率和视角范围,形成防眩等功能。偏光片是一种产生和检测偏振光的片状光学材料,也是液晶显示屏必不可少的关键组件。
液晶屏使用功能不同,采用的偏光片也不尽相同。偏光片按功能分类有透射式偏光片、反射式偏光片、半透过半反射式偏光片、补偿型偏光片等;按附加功能分类有防炫目(AG) 、放划伤(HC) 、防反射/低反射(AR/LR) 、防静电(Anti-Static) 、防污染(Anti-Smudge) 等。
偏光片本身极易受到水汽和高温的破坏作用,因此在切片和使用过程中,对偏光片结构的任何一些微小的损伤都有可能降低偏光片的耐久性。
1、PVA 膜:POL 核心功能部分,其上有拉伸的分子链能够吸收光线,故当偏振方向垂直于分子链的光才能够全部通过。由PVA 膜制成的偏光层易吸水、褪色而丧失偏光性能,故在PVA膜的两侧分别采用一层光性均匀性、透明性良好的TAC 膜可以隔绝水分和空气,保护偏光层。
2、PSA(Pressure Sensitive Adhesive,压敏胶合剂):一种专用的光学压敏胶,主要起粘接作用。压敏胶合剂要求具有高性能的光学特性、优异的耐湿热性能、良好的再剥离性能、较高的剥离强度、恰当的初粘力和持粘力。
单体透过率(Ts)指单片偏光片的透过率,平行透过率(Tp)指两片吸光轴平行的偏光片叠加后的透过率,直交透过率(Tc)指两片吸光轴直交的偏光片叠加后的透过率,在这三项指标中Tp 和Tc 影响LCD 屏的亮度(L)和对比度(Tp/Tc),对LCD 制造商十分重要,为了获得高亮度高对比度的良好显示效果,希望Tp 尽可能的高而Tc 尽可能的小。偏光度(Polarizing Co-Efficiency,PE)是用来表示偏光片产生偏振光的综合效率,是一个计算值,其计算公式如下:
由上式可得出POL 的偏光度与透过率的关系曲线 所示。由曲线图可以发现,偏光度与透过率成反比。而实际中,偏光度可以做到很高,接近100%。但透过率不可超过50%,因为沿吸收轴方向的光全部吸收,但剩下的50%光还存在少量的反射、散射等。对于普通型偏光片,一般P=90~99%,T=41~44%;中耐久、高对比型偏光片,则P≥99.9%,T≥42%。
2、粘接性。主要是指压敏胶与玻璃基板的剥离力,压敏胶与偏光片剥离膜的剥离力,保护膜与偏光片之间的剥离力。剥离力太大,则该偏光片返工性差。但如果剥离力很小,则易造成偏光片在玻璃基板上贴合后压敏胶耐久性和耐湿性能下降,从而影响偏光片的使用性能。三种剥离力的测定均使用拉力实验机进行测定,对应规格如下表:
3、耐久性:主要是耐湿热性能指标的高低。对于普通型POL:40℃×90%RH;对于中耐久型POL:60℃×90%RH;对于高耐久型POL:70℃×95%RH 以上)。
4、偏光度:样品长70mm,宽50mm,测定其透过率,吸收轴平行时的透过率为H0,垂直时为H90,偏光度V 计算公式:V =(HO-H90)/(H0+H90)X 100%
实验结果:附着水珠部分位置发生偏光片失效;粘贴保护膜位置,将水封住无法挥发出来从而
碘素消失是指碘素从偏光子(吸着碘素的PVA)中流失出来的Mode;偏光片本身的NeutralGray的颜色和偏光性能是因为碘素赋予的,所以碘素消失的地方变成了未吸着碘素以前透明的样子,光学性能丧失。
天马显示屏选用的偏光片供应商为日本三立子(Sanritz);产品规格书如上图所示;行业内车载产品偏光片供应商能够承诺的温湿度条件为60℃,90%RH,500小时;(PS:消规类产品承诺的温湿度为40℃,60%RH)出现问题的样机为水汽未清理完全,相当于湿度100%,属于严重超规的实验,超过了偏光片业内标准,故发生失效。
显示面板的制造过程可分为三大阶段:前段阵列工序(Array), 中段成盒工序(Cell)以及后段模组组装工序(Module)。后段模块组装制程, 是将成盒工序中贴合并切割后的面板玻璃,与其他组件如背光板(LCD专有)、电路、外框等多种零组件组装的生产作业。
技术进程:目前三大工序阶段中,只有模组组装工序所需设备处于技术成熟阶段,较多企业参与竞争,阵列工序及成盒工序还待突破。
阵列工序是在玻璃基板上制造TFT阵列的过程,LCD与OLED的生产工序无重大变化。在成盒工序上,主要是显示功能的实现。LCD是将TFT基板与CF基板拼合,进一步加工成TFT-LCD面板的过程
通过成膜,曝光,蚀刻三道工艺叠加不同图形不同材质的膜层以形成LTPS(低温多晶硅)驱动电路,具有解析度高、反应速度快、亮度高和节省空间等特点。相比非晶硅技术,最大的差别在于成膜时LTPS多了一步结晶工序,因而增加了对结晶炉设备的需求。由于驱动背板上集成多种形状复杂的膜层,本段工艺需要循环12次才能完成,技术难点在于微米级的工艺精细度以及对于电性指标的极高均一度要求。
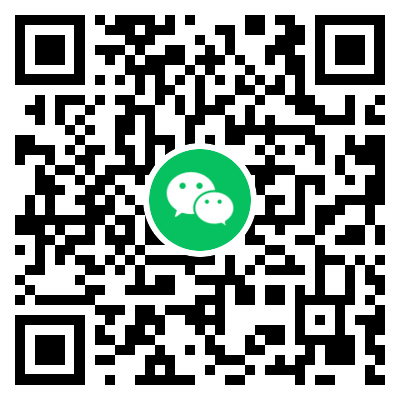